Posts
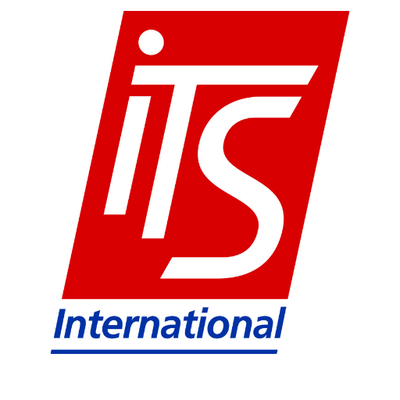
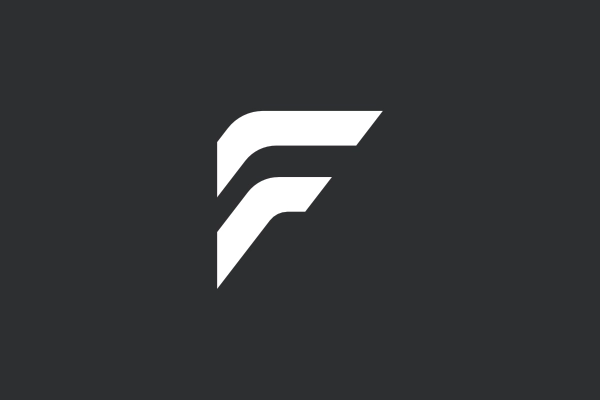
Robotic Research: Harnessing AV Potential
Robotic Research: Harnessing AV Potential
Robotic Research is leading in AV R&D, from work with the US Army to enabling the first automated BRT line in North America: Gordon Feller assesses what the company is doing in ITS International.
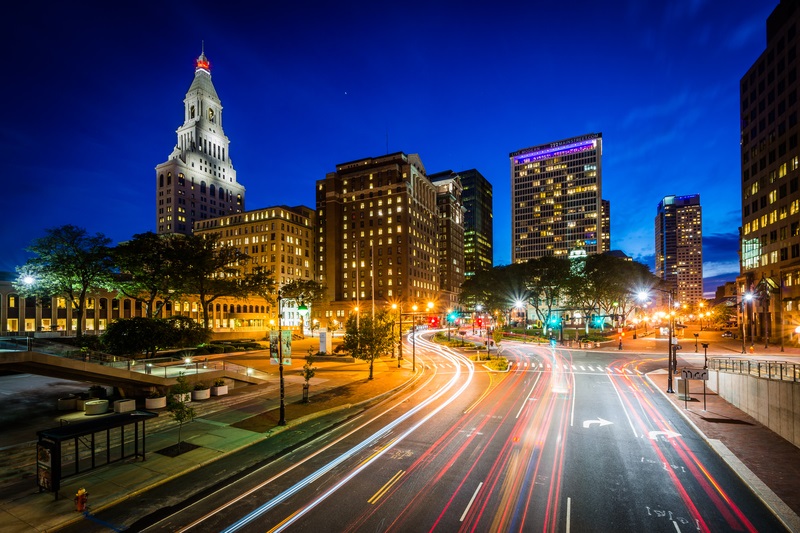
In 2020 the US government set an R&D priority for multiple Federal agencies – some of them civilian, some of them military – to promote automated vehicles (AVs). One special study released by the US National Science & Technology Council and US Department of Transportation helped to specify the focus of the new priority: Ensuring American Leadership in Automated Vehicle Technologies: Automated Vehicles 4.0. The report makes the case for a push into some different R&D domains, suggesting that AVs are likely to play a role in future missions from the Department of Defense (DoD) – and that military research would contribute to AVs’ civilian applications too.
Where exactly is this DoD commitment being made so visible? The race to safe, fully autonomous vehicles is picking up speed. However, for the US Army safety doesn’t just mean avoiding crashes; it means removing the driver from the vehicle altogether. In off-road terrain, GPS-denied environments, and poor weather conditions the US Army is driving driverless autonomous vehicles forward and backwards. Robotic Research is the autonomy provider behind the army’s Leader-Follower programme, the Federal government initiative that marks the Army’s first real fully autonomous military systems. Surprisingly, it’s not from Silicon Valley. Instead, it comes from a company in Clarksville, Maryland.
Tesla and Waymo
Key players like Tesla and Waymo are helping to set the pace for AV development, technological maturity, regulations and safety. So Silicon Valley may appear to be leading the pack - yet thousands of miles away Robotic Research is developing and demonstrating its autonomous technology on OshKosh’s Palletised Load System (PLS) trucks and has already delivered nearly 100 approved AVs. These ruggedised logistics trucks run unmanned in rough terrain, vegetation and dust, which speaks to the leading-edge automation technology that Robotics Research is developing.
The benefit to the Army is immeasurable. Logistical operations, often requiring soldiers to ride in a convoy, are among the more dangerous duties for any soldier. Deploying unmanned convoys provides a life-saving solution to this highly dangerous problem.
Unfortunately, removing the soldiers does little to make these large, slow-moving assets less vulnerable to attack. But for Robotic Research, that just presented another complex challenge. The company recently announced it has added Retrotraverse to its AutoDrive-M autonomy kit, enabling the autonomous reversing of these PLS trucks, even while towing double-hitch trailers – a challenge for even the most seasoned drivers. If a platoon of unmanned vehicles encounters a dangerous situation, the entire convoy can navigate its way out in reverse, regardless of limited clearance they may have or what the trucks have in tow.
The implications for the military are clear. The capability to autonomously drive and reverse a platoon of trucks removes the solider from harm’s way and ensures logistical operations can maintain or improve their efficiency. For other edge case applications like logging or mining, risks in some of the industry’s most dangerous routes can be mitigated and the efficiency of transporting material can be significantly increased.
In the commercial trucking space, much of the interest in autonomy has focused on solving driver shortages and increasing fuel efficiency.
The US Army’s goal to fully remove the driver from logistics trucks is helping to spur innovation and will likely propel the commercialization of this technology for large-scale product transport. But drivers shouldn’t fret. With an emphasis on vehicle-agnostic autonomy, reversing technology, and navigating in GPS-denied environments, companies like Robotic Research are helping to eliminate the pain points of drivers, not their jobs. With roughly 67% of trucking accidents happening in parking lots, the ability to let autonomy take the wheel when entering a lot or yard could be a dream come true for many drivers, businesses and insurance companies.
Autonomous technology provider
As an autonomous-technology provider, Robotic Research is also helping Connecticut Department of Transportation (CTDoT) make historic advancements in automated public transit thanks to a new programme funded by the USDoT. Through the Federal Transit Administration's Integrated Mobility Innovation (IMI) initiative, Robotic Research’s proprietary AutoDrive advanced driver-assistance system is enabling the automation of heavy-duty transit buses for revenue service deployment. This innovation will be a first for mass transportation systems in all of North America.
When the programme launches for public use, three 40-foot, automated, electric New Flyer Xcelsior Charge heavy-duty transit buses will be operating on the CTfastrak corridor, a dedicated nine-mile stretch for exclusive use by CTtransit buses. The bus operations will be a zero-emission deployment running between New Britain and downtown Hartford.
This pioneering operation will utilise automated technology to improve transportation accessibility for passengers with disabilities while improving efficiency and the rider experience for all passengers.
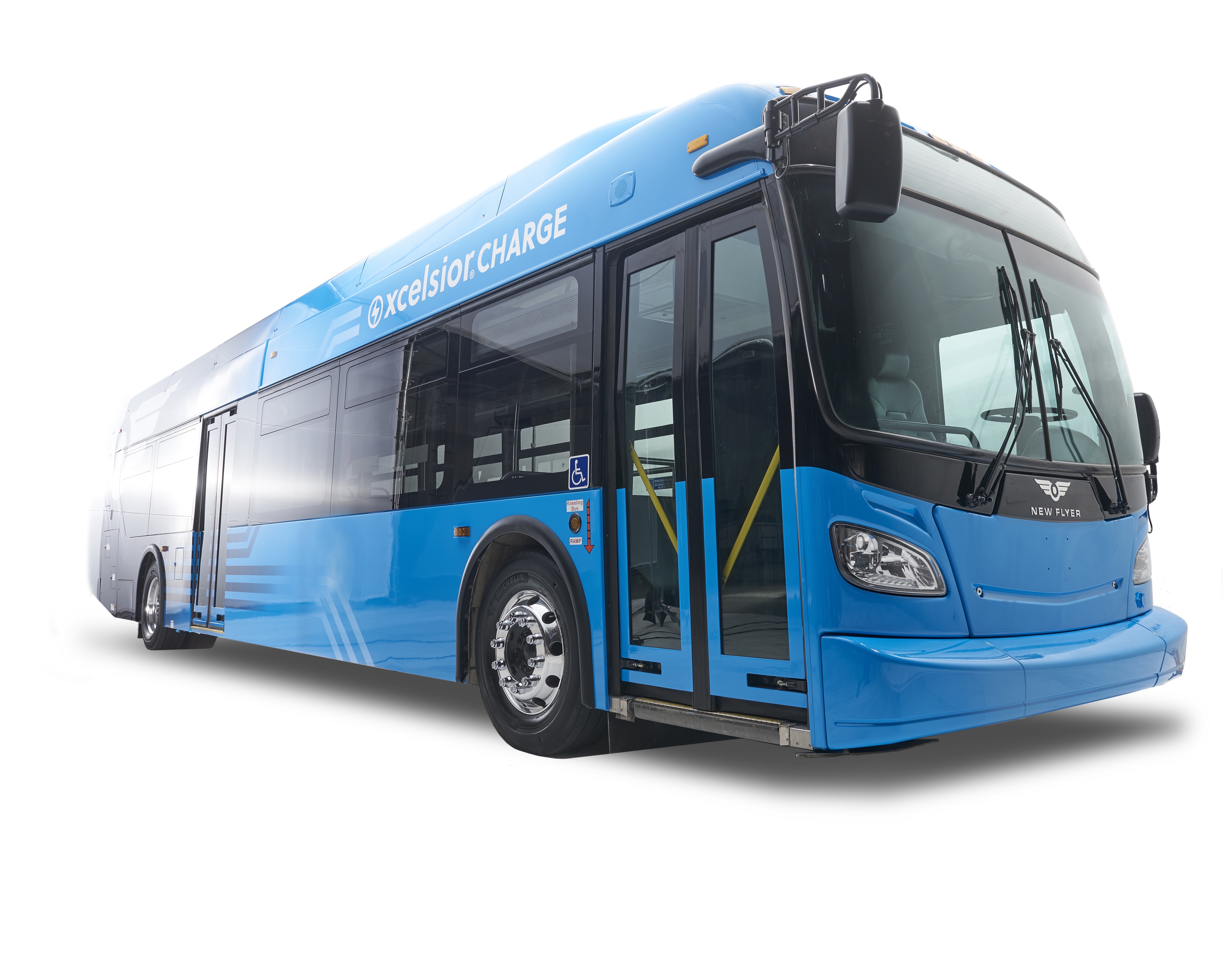
As the first automated Bus Rapid Transit line put into revenue service in North America, the CTtransit initiative also marks the first application of automated precision docking to minimise platform gaps, ensuring boarding is compliant with the Americans with Disabilities Act (ADA) of 1990 - which prohibits discrimination based on disability such as blindness – and increasing accessibility for all passengers.
The automated driving objectives of this project also include the demonstration of platooning capabilities to maintain more efficient headways between buses.
Connecticut is one of 23 US states now receiving IMI funding, which aims to advance mobility through creative partnerships and emerging technologies, combining public and private transportation assets and strategies to increase access to mobility for everyone.
The team for this project is led by CTDoT and also supported by New Flyer of America and the non-profit Center for Transportation and Environment.
Future of mass transit
Automated buses have great potential in public transportation, New Flyer thinks. “The technology is real and it’s here,” said company president Chris Stoddart.
He anticipates that fleets of automated buses will improve road safety, shorten commute times, increase energy efficiency and reduce congestion.
“As standards and regulations are developed and implemented and automated buses are deployed across North America, we expect our Xcelsior AV to enable meaningful improvements in the public transit user experience, which will hopefully lead to increased ridership,” he continues. “Together with Robotic Research, we are leading clean, accessible, reliable mobility that’s safer for all.”
Alberto Lacaze, Robotic Research’s president, speaks of his excitement for future collaboration and joint work on public transportation and autonomous technology. “Welcome to the future of mass transit,” he said. “Automated transit buses, like the Xcelsior AV, are not just safer and greener, but more efficient. By optimising rider capacity, improving traffic flow, and reducing stop-and-go accordion delays, these vehicles have the potential to not only increase the efficiency of travel for those on board, but for all vehicles on the road.”
ABOUT THE AUTHOR
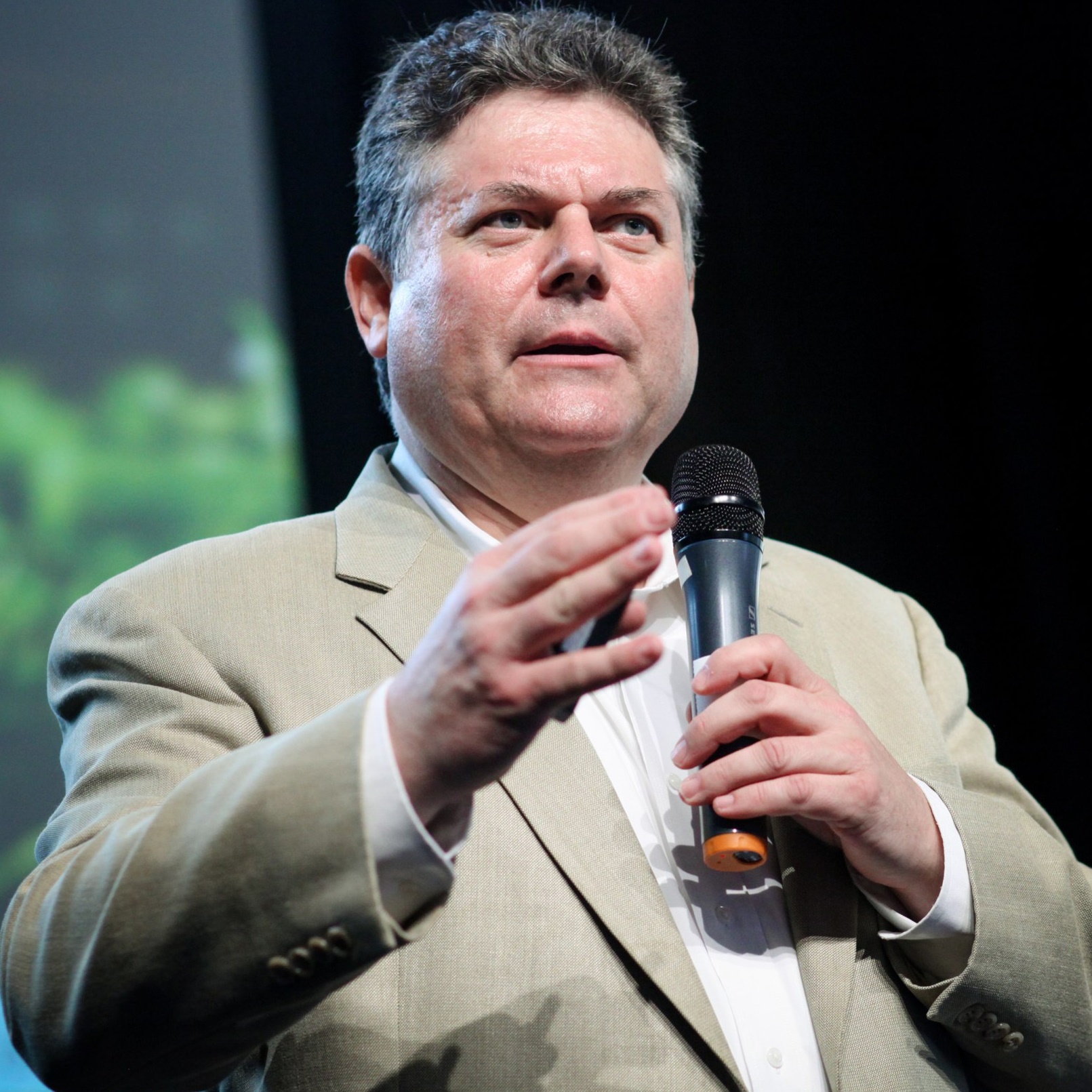
Robotic Research and New Flyer
Robotic Research provides autonomy software and robotic technology and solutions, and has been collaborating with bus company New Flyer as its exclusive autonomous technology partner supporting its automated technology programme.
New Flyer is North America’s heavy-duty transit bus leader, whose Xcelsior and Xcelsior Charge brands incorporate a broad range of drive systems, including clean diesel, natural gas, diesel-electric hybrid, trolley-electric, battery-electric, and fuel cell-electric.
Robotic Research’s AutoDrive ADAS technology is platform-agnostic and can be used to retrofit vehicles of all sizes, from small, portable robots to large trucks and buses. The system provides autonomous functionality on surfaces ranging from urban-improved roads to off-road terrain, all while the vehicle is collecting and analysing data to enhance the future of transportation.
Robotic Research has deployed SAE Level 4 automated vehicles into multiple operating environments across the US and around the world, including urban commercial centres, military bases and government sectors. The company’s ADAS technology is currently operating in 30 states and on four continents.
New Flyer parent NFI Group provides a suite of mass transportation solutions under various brands, manufacturing approximately 8,800 buses and coaches annually, actively supporting over 105,000 buses and coaches currently in service throughout the world and delivering electric buses to multiple US properties.
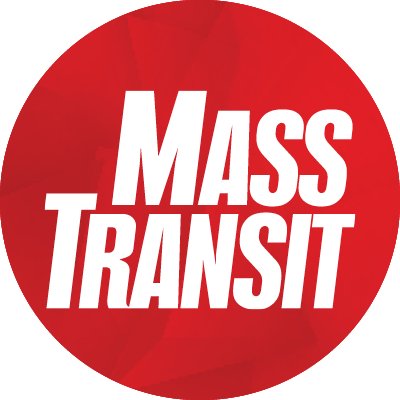
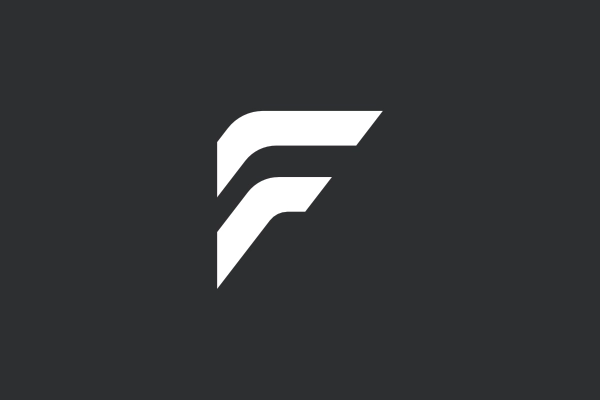
ABRT: Reducing Congestion, Costs while Improving Safety, Efficiency
ABRT: Reducing Congestion, Costs while Improving Safety, Efficiency
Automated Bus Rapid Transit represents an innovation that promises to reduce operating costs while delivering benefits, but support is needed from transit agencies and policymakers.
Jun 8th, 2021
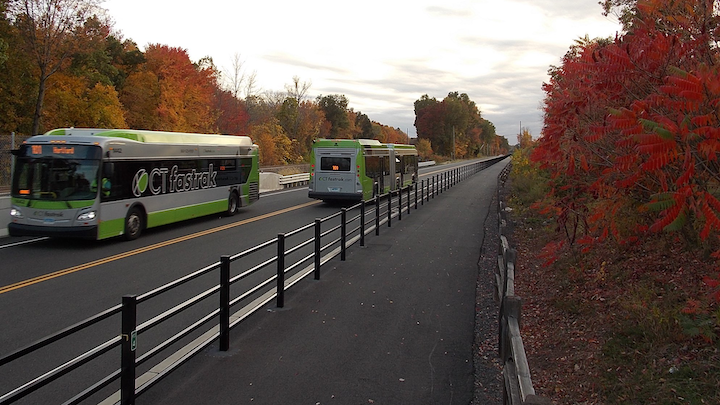
In June 2020, the Connecticut Department of Transportation announced plans to test North America's first full size automated transit bus project.
CTDOT
Municipal transit authorities are struggling with a variety of issues, including aging infrastructure and declining ridership. Transit authorities are at a transformative point. The question is whether they use the same existing service model or embrace technology to help solve many of their problems. I believe transit authorities should embrace this transformational tipping point to embrace technology as it will make them more efficient, easier to operate and improve the quality of service, all while cutting operating costs.
Automated Bus Rapid Transit (ABRT) is a technology solution that promises to reduce operating costs while delivering benefits such as reducing headway, improving on-time service, providing better passenger safety and offering easier access for handicapped passengers. Advanced Driver Assistance Systems (ADAS) is being added in new bus models or retrofitted to existing bus fleets to provide automated features such as collision avoidance, lane assist, precision docking and other features to assist bus drivers.
ARBT also requires action from policymakers. Policymakers need to dedicate funding, which has and remains an issue for all transit authorities, but they must also take action by creating dedicated bus lanes and synchronized traffic controls. Once established, bus platooning technology makes it easier to scale service to accommodate more passengers when needed. Platooning also can improve safety by spreading passengers among multiple buses to maintain social distancing to prevent COVID-19 exposure.
ABRT promises to improve bus transit in various ways, but there are three primary areas where automation can have a real impact on transit service: increasing efficiency, optimizing costs and improving safety.
How ABRT Increases Transit Efficiency
Recent research from the Eno Center for Transportation titled, “A Budding Model: Los Angeles's Flower Street Bus Lane,” shows the benefit of installing bus lanes. Eno studied the effects of a 1.8-mile, peak hour bus lane installed by Los Angeles County Metropolitan Transportation Authority (L.A. Metro), in partnership with the
Los Angeles Department of Transportation (LADOT). Although installed as a temporary measure to address traffic delays due to rail station closures, it had a big impact. Specifically, the research found:
“[T]he bus lane greatly improved mobility, accounting for more than 80 percent of people moving in the corridor, or around 10,000 bus riders a day during the peak-hour period. Person-throughput increased 37 percent compared to pre-traffic conditions with limited reduction of the capacity in general use lanes for private vehicles. Two-thirds of bus customers and two-thirds of operators reported time savings. This perceived time savings is consistent with observed travel times, which improved up to 30 percent throughout the corridor.”
Keep in mind, this was not with an automated bus.
Automated buses are ideal for fixed-route bus systems that operate 50 percent or more of their route on a dedicated guideway. These systems tend to have defined passenger stations, traffic signal priority and a short headway providing bidirectional services during peak hours on weekdays.
For example, the Connecticut Department of Transportation (CTDOT) is testing automated technology on its CTfastrak bus rapid transit corridor, one of its most heavily traveled routes between New Britain and Hartford. The CTDOT system uses an express bus lane for its CTfastrak service, which makes it a good candidate for automated bus technology. New Flyer buses equipped with Robotic Research’s AutoDrive® advanced driver-assistance system are being placed into service to automate features such as steering, which reduces operator stress. Incorporating a drive-by-wire system to automate control of the brakes, steering and throttle enables automated lane-keeping that helps drivers keep buses centered in the lane. This can be a real stress-reducer for operators and a technology that makes narrower lanes more practical.
Connected vehicle communications also opens new possibilities to increase passenger capacity while controlling costs. Bus platooning, sometimes called “leader-follower,” can be used to create bus platoons to increase capacity during peak times, making it possible to move more buses while reducing headway. The Port Authority of New York and New Jersey is experimenting with platooning to increase rush-hour capacity on the approach to Lincoln Tunnel.
Greater Cost Efficiencies with ABRT
Adopting ABRT offers transit authorities many cost-saving benefits, as well, especially when compared to alternative strategies such as light rail. Automated buses don’t need a dedicated rail system or a dedicated right of way. Buses can use the existing roadways, or they can use dedicated lanes to create temporary transit systems at peak times and then revert to handle normal traffic the rest of the time.
Automated buses can help reduce the amount of training required to perform difficult maneuvers, like precision docking, which is particularly useful for articulated buses where it is difficult to align the rear doors to the platform stop,by adding automating these functions. . Automated precision docking also reduces damage to vehicles and transit stops, which not only reduces repair costs but also cuts insurance costs.
Using automated controls to guide the bus for precision docking ensures that passengers with mobility devices or disabilities can board every time. Precision docking aligns the bus for level boarding for all riders and that the gap is no more than three inches in compliance with the Americans with Disabilities Act. When you consider that the Federal Transit Administration (FTA) estimates that the average BRT trip cost is $3.43 while the average cost for accessible service (i.e., demand-responsive paratransit) is $39.51 per trip, being able to accommodate more passengers with disabilities using conventional buses can generate substantial financial returns.
Automation Improves Safety
Automation can improve bus safety by augmenting the operator’s eyes and ears. ABRT reduces mishaps and accidents by helping the driver overcome blind spots and “see” potential hazards before there is an accident.
Automated bus technology is playing an increasingly important role in collision avoidance. In 2018, U.S. transit agencies reported 4,676 bus collisions, 16,348 injuries, 84 fatalities and $684 million in liability expenses. What’s more, 74 percent of high-value bus claims (over $100,000) were related to collisions.
To increase safety and eliminate costs from accidents, automated collision avoidance systems are being installed to assist operators by providing visibility in blind spots. Imaging sensors, such as cameras, radar and LIDAR (light detection and ranging), can now generate a real-time virtual model of the area surrounding the bus, detecting encroaching traffic or pedestrians. The same technology can be used to monitor problem areas, such as rear entry doors, which can be especially hazardous.
These same sensor systems can not only alert the driver to potential obstacles, but they also can be linked to bus braking and steering using drive-by-wire installations. Avoidance and Emergency Braking (AEB) systems have become common in passenger cars and are increasingly being used in transit buses to prevent collisions with pedestrians, cyclists and other vehicles that share the road. Furthermore, automated braking and acceleration also provide smoother stops and starts which generate a more comfortable ride while reducing passenger falls.
These are just three areas where automation will transform bus transit systems. As with all robotic technology, the objective is to make the operator’s life easier. Automation enhances driver capabilities, removing stress from bus operations by offering assistance with tough tasks such as docking alignment, monitoring blind spots and supplementing bus operations with automated safety systems like AEB.
And the good news for bus transit authorities is this technology is available today. Transit operators such as CTDOT and the Kansas City Area Transportation Authority are procuring new buses and retrofitting buses already in service with new sensors and drive-by-wire technology. And as the technology continues to become more sophisticated and more cost-effective, expect to see more ABRT systems emerge in the near future.
---------------
Alberto Lacaze is the co-founder and president of Robotic Research and a recognized expert in robotic engineering.
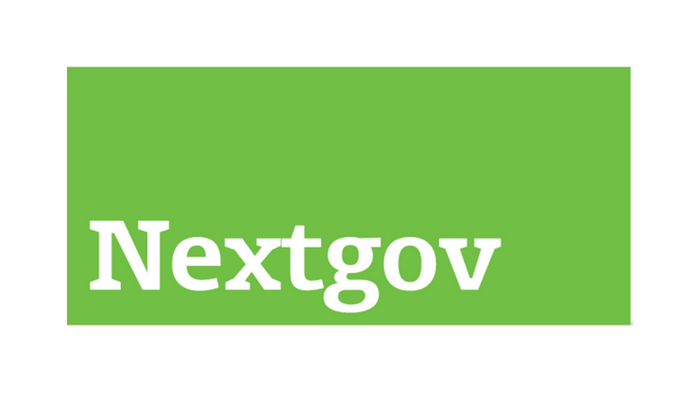
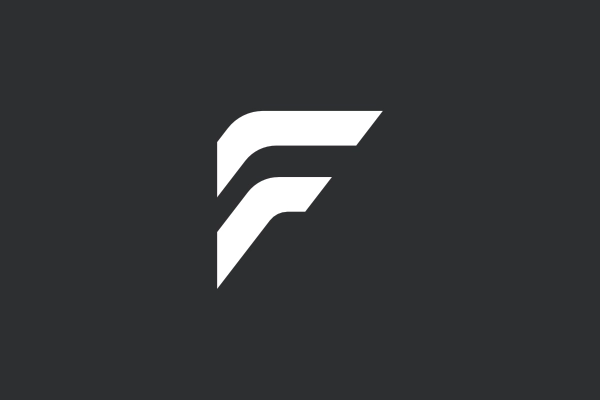
Pentagon Experiments with Self-Driving Shuttles at San Diego Military Base
Pentagon Experiments with Self-Driving Shuttles at San Diego Military Base
Driverless technology provider Robotic Research and Verizon Public Sector on Wednesday confirmed their cooperative involvement in a pilot project to explore the use of autonomous shuttles at the Marine Corps Air Station, or MCAS, Miramar’s 5G Living Lab in San Diego.
NavalX SoCal Tech Bridge, US Ignite and Local Motors are also involved in this 90-day experiment with self-moving shuttles to transport people and packages around the military installation.
“This pilot is one example of how 5G-enabled applications carry the potential of enhancing operational effectiveness,” Verizon’s Senior Vice President of Public Sector Jennifer Chronis told Nextgov Wednesday.
The announcement comes almost a year after Verizon and MCAS Miramar unveiled their plans to deploy the former’s 5G Ultra Wideband on a military base for the very first time. Working with a range of strategic partners, they’ve since started to demonstrate 5G-enabled innovations across artificial intelligence, self-driving vehicles and drones in real-world scenarios at the living lab. Broadly, those involved are assessing the benefits such next-generation wireless capabilities can bring to public safety, commerce and energy management.
“Working in conjunction with our partners in the Marine Corps at Miramar, we have created a true testbed for innovation—innovation that will have tremendous impact within the Department of Defense and across the public sector,” Chronis said.
This endeavor is new, but Chronis added that Robotic Research’s “commitment to MCAS Miramar began far before this pilot.” The company has been providing the Pentagon with autonomous technology solutions for nearly 20 years. In particular, she noted it specializes in “platform-agnostic autonomy,” enabling the automation of “a wide variety of platforms for both government and commercial customers.” In 2017, the Maryland-based company became the Autonomy Strategic Partner for the Marine Corps autonomous proving grounds at MCAS Miramar.
“This initial partnership led to additional collaboration focused on the use of autonomous technology on both the battlefield and installations,” Chronis said. “Current efforts include the unmanned logistics systems prototype being developed as well as the trial of low-speed autonomous shuttles doing package delivery on base.”
Through this fresh pilot, Robotic Research’s AutoDrive autonomy kit provides the self-driving capabilities of Local Motors’ autonomous shuttle, Olli, rolling through the military installation. Verizon’s 5G will transmit the heaps of system and sensor data collected by the shuttle back to a storage service, which is also provided by Robotic Research.
“Understanding the operational needs of our partners in the Marine Corps is a top priority,” Chronis noted, “and learning how 5G UWB, in conjunction with autonomous vehicle technology and real-time sensor data, can be leveraged to make package delivery more efficient across multiple scenarios—from tools to the flight line, to mail delivery, to product for retail environments—is a step forward in addressing the digital transformation needs at Miramar, and beyond.”
Generally, autonomous shuttles currently operate with an onboard safety operator. But one element the partners mentioned exploring in this project includes approaches where one person monitors a single fleet remotely, from a centralized location.
Verizon and Robotic Research are slated to showcase some of what’s to come during the Electric Mobility Symposium at MCAS Miramar on June 24.
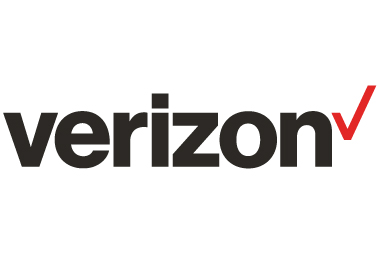
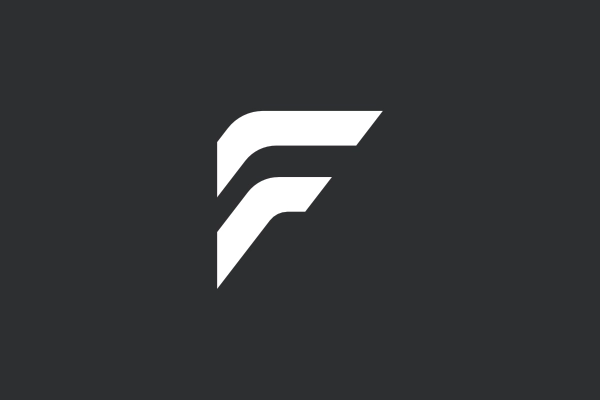
Robotic Research, Verizon collaborate on autonomous shuttles at MCAS Miramar
CLARKSBURG, Md.–(BUSINESS WIRE)–Robotic Research, LLC (rr.ai), a global leader in autonomous driving technology and solutions, and Verizon Public Sector, a key Department of Defense digital transformation partner, announced today their joint support of an autonomous shuttle pilot project with US Ignite, Local Motors, and NavalX SoCal Tech Bridge as part of the 5G Living Lab at U.S. Marine Corps Air Station (MCAS) Miramar, in San Diego.
As part of the 90-day pilot, Robotic Research is providing the autonomous driving technology for Local Motors’ autonomous shuttle, Olli, transporting people and packages around MCAS Miramar, leveraging Verizon’s 5G Ultra Wideband to transmit the vast system and sensor data collected by the shuttle back to Robotic Research’s nSight™ Vault storage service.
“Once the data is uploaded to nSight Vault through Verizon’s 5G network, our nSight Review system monitors health and performs data analytics to continuously improve the operation of the autonomous shuttles,” said Joe Putney, Director of Commercial Systems at Robotic Research. “We really benefit from Verizon’s 5G service at MCAS Miramar providing real-time access to the large amounts of data generated by the system.”
Verizon Public Sector and MCAS Miramar announced the first-ever 5G Ultra Wideband deployment on a military base last July. Since then, in collaboration with a number of strategic partners, they have created a true testbed for innovation, exploring 5G-enabled innovations across autonomous vehicles, artificial intelligence, and drones.
Robotic Research officials see the nationwide rollout of 5G as creating huge opportunities for autonomous vehicles by enabling higher-bandwidth and real-time sharing of data between vehicles and between vehicles and infrastructure. Among the other areas of focus being pursued, the 5G Labs team within Verizon is exploring the benefits of 5G around public safety, frictionless commerce, and energy management.
“We have worked collaboratively with the NWIC Pacific team to create a true testbed for innovation at MCAS Miramar,” said Jennifer Chronis, Senior Vice President of Public Sector at Verizon. “Leaders across the Department of Defense understand the mission-critical role 5G plays in unlocking innovation for the military, and strategic partners like Robotic Research are bringing to life some of the exciting technologies that are possible when you integrate 5G.”
One area of innovation includes onboard safety attendants. Currently, in most autonomous shuttles, there is a steward who monitors the health and status of the vehicle. But as the autonomous industry continues to mature, it could follow a similar model to that of home security systems.
“Rather than having a security guard in your home, there is a security system that provides information to a centralized location, where a single person can monitor many homes simultaneously,” Putney said. “Similarly, you could have automated vehicles sharing data with a centralized monitoring station, so a single person can monitor and control a fleet of vehicles.”
All that is required is a reliable data backbone, and Robotic Research officials see Verizon’s 5G network as the next step in the right direction.
Both Robotic Research and Verizon will be showcasing the benefits of combined 5G and autonomous mobility during the Electric Mobility Symposium, June 24th at MCAS Miramar.
About Robotic Research
Robotic Research is U.S.-based, global leader in localization, autonomy, and robotic technology transforming the way we move. Founded in 2002, the Company has been a trusted technology partner to the public and private sector for nearly twenty years. From people to platforms, at home or overseas, Robotic Research is driven to make the way you move smarter, safer, and more efficient.
To learn more about Robotic Research, visit www.rr.ai, and follow us on Twitter and LinkedIn.
Contacts
Taylor Smith
Press@rr.ai
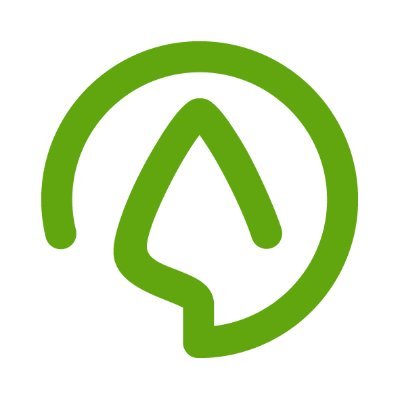
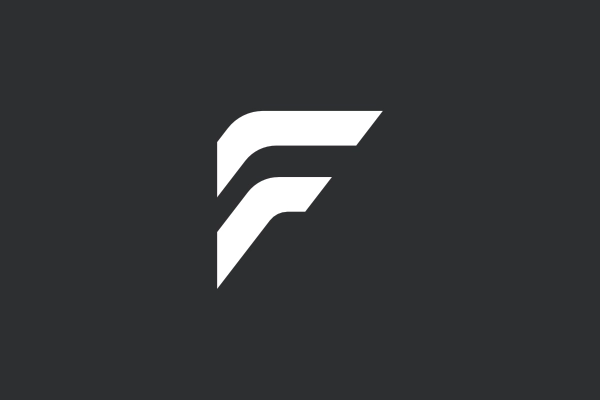
Robotic Research and FPInnovations Partner to Develop Resource Road Truck Platooning Technology
ROBOTIC RESEARCH AND FPINNOVATIONS PARTNER TO DEVELOP RESOURCE ROAD TRUCK PLATOONING TECHNOLOGY
Joint efforts will provide Level 4 Autonomy for natural resource sector roads
CLARKSBURG, Md. and MONTRÉAL–(BUSINESS WIRE)–Robotic Research, LLC (rr.ai), a global leader in Automated Driving Systems (ADS), and FPInnovations, a Canadian private non-profit research and development center, announced today their collaboration to develop an off-road truck platooning system for the forest industry. This project will combine Robotic Research’s proven expertise as a global leader in self-driving technology with FPInnovations’ knowledge in forestry and transportation to adapt the truck platooning technology to off-highway environments.
The multi-year project aims at accelerating the adoption of off-road automated-vehicle (AV) technology to improve safety and address an acute labor shortage, thereby improving the quality and viability of rural jobs where natural resources are located. Looking to the future, a successful project would not only benefit Canada’s forest industry, but other Canadian sectors such as mining resources and natural resources in Northern Canada.
Robotic Research, with a history of other groundbreaking projects, including the development of the Xcelsior AV announced with New Flyer this year, will create unmanned convoys of Class 8, ADS-enabled trucks that follow a driver in a lead vehicle. The project will adapt existing technology to challenging Canadian conditions such as four-season weather and operations on off-pavement roads, particularly for resource roads in continental and polar climates.
“We are extremely proud to have been selected by FPInnovations and believe this project is a transformative model of how ADS can aid industries, like forestry, operating in perilous conditions or facing workforce shortages.” said Alberto Lacaze, President, Robotic Research. “The unmanned truck convoys work in concert with commercial drivers to enhance their efficiency, while also protecting their safety.”
In Phase I, truck convoys will be put through safety trials that mimic the routes from harvesting sites to sawmills. Once the system is proven to be secure, FPInnovations will run trials on actual resource roads, known to be challenging because of dust, sharp curves, and steep slopes.
“We are very pleased to partner with Robotic Research whose leading-edge expertise in the commercial on-road and defense transportation will greatly benefit Canada’s natural resource sectors and help address an acute labor shortage” stated Stéphane Renou, President and CEO, FPInnovations.
About Robotic Research
Robotic Research is U.S.-based, global leader in localization, autonomy, and robotic technology transforming the way we move. Founded in 2002, the Company has been a trusted technology partner to the public and private sector for nearly twenty years. From people to platforms, at home or overseas, Robotic Research is driven to make the way you move smarter, safer, and more efficient.
About FPInnovations
FPInnovations is a private not-for-profit research and development center with professional researchers who create solutions in support of the Canadian forest sector’s global competitiveness. It is ideally positioned to perform state-of-the-art research, develop advanced technologies, and deliver innovative solutions to complex problems for every area of the sector’s value chain, from forest operations to consumer and industrial products. Its R&D laboratories are located in Québec City, Montreal, and Vancouver, and it has technology-transfer offices across Canada.
Related links:
To learn more about Robotic Research, visit www.rr.ai, and follow us on Twitter and LinkedIn.
To learn more about FPInnovations, visit web.fpinnovations.ca, Twitter, LinkedIn, and Facebook.
Contacts
Taylor Smith
press@rr.ai
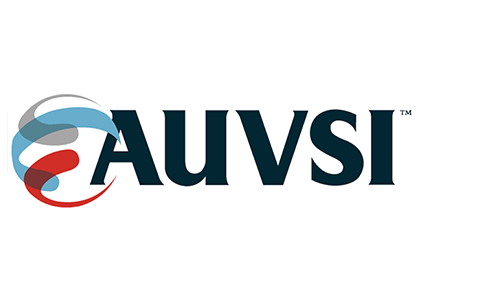
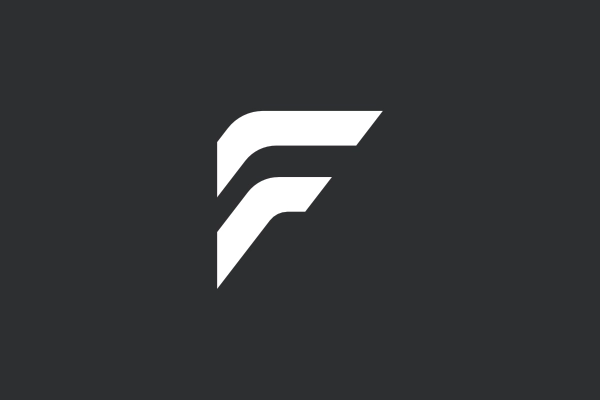
Robotic Research Announced as Finalist for AUVSI XCELLENCE Awards
Robotic Research Announced as Finalist for AUVSI XCELLENCE Awards
CLARKSBURG, Md.--(BUSINESS WIRE)--Robotic Research, LLC (rr.ai), a global leader in autonomous technology, announced today it was named by the Association for Unmanned Vehicles Systems International (AUVSI) as a finalist for an XCELLENCE Award in the category of Innovation.
AUVSI selected Robotic Research for its Pegasus Mini, a lightweight, compact unmanned system that can fold out of a backpack and transform from a tracked ground robot to quadcopter-type drone, and then back again.
“Pegasus Mini, as well as our whole Pegasus family of systems, was designed with the user in mind, as a way to overcome the challenges faced by legacy systems,” said Alberto Lacaze, co-founder and president of Robotic Research. “So, it’s very gratifying to be nominated as a finalist for an AUVSI XCELLENCE Award.”
AUVSI represents the unmanned industry. The XCELLENCE Awards are, therefore, the industry honoring peers—individuals and organizations—that have demonstrated a commitment to advancing autonomy, leading and promoting safe adoption of unmanned systems, and developing programs that use these technologies to save lives and improve society.
“During the last year, the unmanned systems industry rose to meet urgent new challenges posed by the pandemic. It is inspiring to see organizations and companies that led this charge among the XCELLENCE Awards finalists,” said Brian Wynne, President and CEO of AUVSI. “As unmanned systems become increasingly integrated within our society, AUVSI is pleased to recognize this distinguished group for their innovative work that will accelerate our industry forward toward assured autonomy.”
Winners will be announced during an awards ceremony at the AUVSI XPONENTIAL trade show, held on August 16-19, at the Georgia World Congress Center (GWCC), in Atlanta, Georgia.
About Robotic Research
Robotic Research is a U.S.-based global leader in localization, autonomy, and robotic technology transforming the way we move. Founded in 2002, the company has been a trusted technology partner to the public and private sector for nearly twenty years. From people to platforms, at home or overseas, Robotic Research is driven to make the way you move smarter, safer, and more efficient.
To learn more about Robotic Research, visit www.rr.ai, and follow us on Twitter and LinkedIn.
About AUVSI
The Association for Unmanned Vehicle Systems International (AUVSI)—the world's largest non-profit organization dedicated to the advancement of unmanned systems and robotics—represents corporations and professionals from more than 60 countries involved in industry, government and academia. AUVSI members work in the defense, civil and commercial markets. For more information, visit AUVSI.org.
About XPONENTIAL
AUVSI XPONENTIAL is the largest, most significant event for the unmanned systems industry. The 2021 exhibit hall will showcase hundreds of cutting-edge companies from around the world and the conference will feature educational programming by unmanned systems experts, providing information about the future of policy, technology and business solutions and trending topics.
Contacts
Taylor Smith
press@rr.ai