Posts
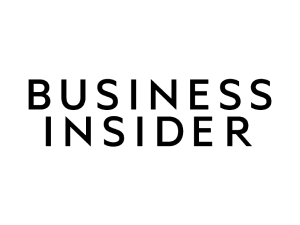
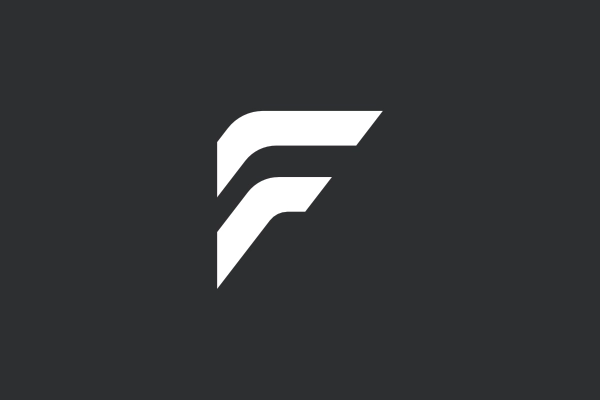
35 under 35: Meet the rising stars of the self-driving industry, from companies like Waymo, Cruise, and Zoox
Insider considered nominations from across the AV industry, limiting the pool to those 35 or younger at the beginning of 2022. From nearly 100 submissions, they selected 35 young professionals as particularly impressive and most likely to someday become household names.
Included on their list was RRAI’s Chief of Staff, Taylor Smith Baisey.
Taylor is an asset to the entire RRAI and Robotic Research team and we are thrilled to see her accomplishments recognized by Business Insider.
Congratulations Taylor!
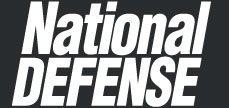
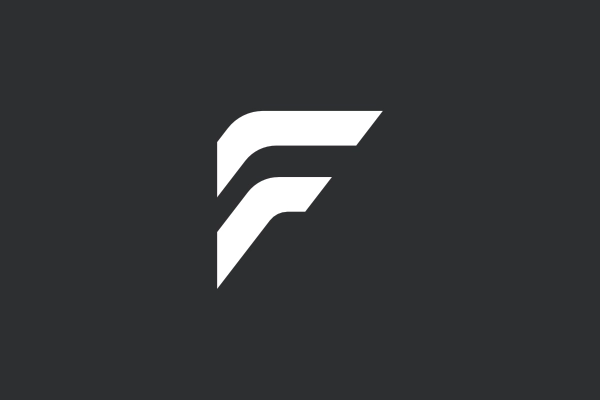
Army Sees Progress with Leader-Follower Vehicle Technology
Army Sees Progress with Leader-Follower Vehicle Technology
1/21/2022
By Yasmin Tadjdeh
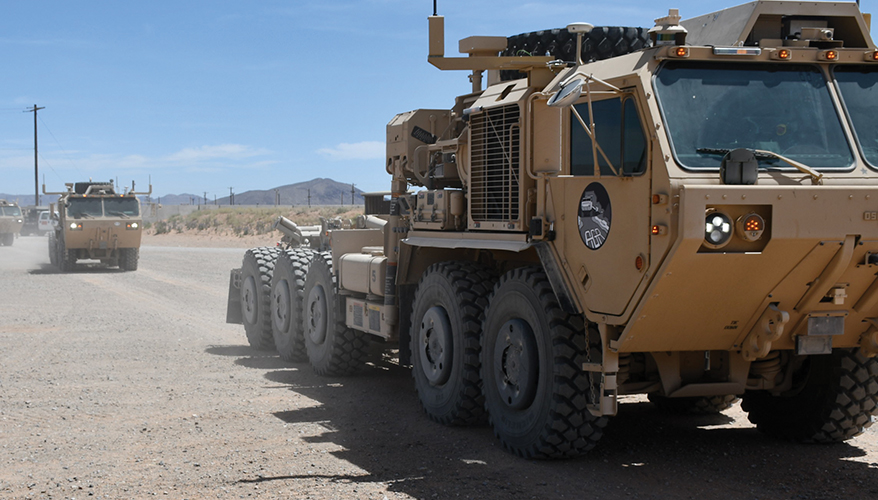
The Army is attempting to leverage robotics and other capabilities to enable its “leader-follower” concept for vehicle convoys. After years of work, the Army has made strides in developing the technology.
At the height of the wars in Iraq and Afghanistan, roadside bombs planted by insurgents maimed and killed servicemembers and civilians alike, targeting vehicle convoys ferrying troops and supplies to bases.
To deal with the threat more immediately, the military invested billions of dollars into uparmored, mine-resistant vehicles that could withstand blasts better. At the same time, it kicked off an ongoing, long-term effort to build autonomous “leader-follow” tech that could cut down on the number of soldiers in harm’s way in future fights as well as free up troops for other tasks.
The service is demonstrating progress. It has tested its leader-follower autonomy software at events such as Project Convergence 2021, where the Army tried out technology that can support its offering for the Pentagon’s joint all-domain command and control concept. Additional work is being conducted at bases such as Fort Polk, Louisiana, and Fort Sill, Oklahoma.
The Army has primarily been using what it calls palletized load systems, or PLS, unmanned follower vehicles, during its experiments, said Maj. Benjamin Hormann, expedient leader-follower project officer at Combat Capabilities Development Command’s Ground Vehicle Systems Center. Soldiers from the 41ST Transportation Company currently own 60 M1075 PLS trucks that are equipped with an autonomy system.
“The unit received new equipment training over two years ago and has implemented a ‘train-the-trainer’ strategy in order to maintain proficiency throughout the year,” he said in an email. “This unit provides real-time feedback to software developers and engineers that get them the capability they want/need very quickly.”
The vehicles are currently using a software version known as LF 1.3.
The Ground Vehicle Systems Center is employing what it calls an “engineering in the dirt concept” where soldier feedback is run through an agile software sprint to develop and update the system every 90 days, Hormann said. Meanwhile, the unit also provides information so requirements and doctrine can be updated.
The Army showed off its expedient leader-follower technology at the service’s Project Convergence exercise at Yuma Proving Ground, Arizona, this past fall, he said. The annual experiment has been called a “campaign of learning” by officials and is meant to contribute to the Pentagon’s JADC2 effort, which aims to better link sensors and platforms into an operating network.
At Project Convergence, officials employed two versions of its autonomy software and completed more than 3,000 miles of robotics testing, Hormann said. The autonomy system was tested on palletized load system trucks, the cold weather all-terrain vehicle and the logistics vehicle system replacement platform.
The Army plans to test leader-follower technology at Project Convergence 2022 with an autonomous missile launcher demonstrator as part of an effort with Army Futures Command’s long-range precision fires cross-functional team and DEVCOM’s Aviation and Missile Center, Hormann said.
Meanwhile, the service recently completed the final increment of capability improvements for its expedient leader-follower program, he said.
For example, the service merged existing autonomy software with a government-owned Robotic Technology Kernel, he said. RTK is the Army’s library of modular software packages that can be used for common ground autonomy software. The software is based on what is known as the Robotic Open System Architecture-Military.
The most recent increment also developed a feature known as “assembly and disassembly” where autonomous PLS trucks could form into a column formation based on orders from a user, as well as “park” the platforms into a line, whether it be from front-to-back or side-to-side, he added.
Another new capability is a “retrotraverse” feature with trailers, which allows the PLS vehicle to reverse and employs what Hormann called a “pin-and-pin-out function.”
This capability allows “the warfighter to back up an autonomous convoy with a trailer without having to get out and put the trailer traversing table locking pin in,” he explained.
Coming up next for the leader-follower program is Army Test and Evaluation Command safety testing for maturation of its software version 2.0 system.
Over the next two years, the 41st Transportation Company is set to participate in three Collective Training Center exercises with leader-follower technology, Hormann added.
The GVSC and product management office for robotic autonomous systems also plan to further mature the technology’s software and hardware, he noted. This includes increased reliability and further hardening of the system.
The Army is currently using a “buy, try, decide” procurement model and a mid-tier acquisition rapid fielding approach when it comes to acquiring the systems, he said.
“There will be a later decision point to increase capability and mass produce the optionally manned leader-follower system for the PLS program of record,” Hormann noted.
The Army has been working on autonomous military vehicles since 1999, he said. Some of the platforms the technology has been tested on includes Humvees, HX60 tactical trucks, RG-31 mine-resistant ambush-protected vehicles, medium tactical vehicle replacement systems, M915 tractor trucks, medium tactical vehicles, LMTV light utility trucks and heavy equipment transporters.
More recently, the autonomy hardware and software systems developed through the Ground Vehicle Systems Center include the palletized load system, the cold weather all-terrain vehicle, the high mobility artillery rocket system as well as the Marine Corps’ logistics vehicle system replacement platform and the Corps’ Joint Light Tactical Vehicle Rouge Fires variant, Hormann said.
One company that has been working with the Army on leader-follower technology is Clarksburg, Maryland-based Robotic Research.
In 2018, the Army awarded the firm a three-year, $49.7 million contract to provide autonomy kits for large convoy resupply vehicles as part of the expedient leader-follower program. Robotic Research has had its participation extended with various National Advanced Mobility Consortium contract vehicles, said Jim Frelk, the company’s senior vice president. It is currently offering the service technical support on the expedient leader-follower effort.
The organization has been working alongside vehicle manufacturers such as Oshkosh Defense to outfit platforms with its leader-follower autonomy software in places such as Fort Polk, Fort Sill and Camp Grayling, Michigan, for testing. The company provides the autonomy software and Oshkosh provides the drive-by-wire kit for the vehicles, he said.
The company has been working on capabilities such as “safe harbor” features, he noted. Safe harbor functions tell platforms what they should do if there is an attack or breakdown in the systems’ sensors.
Leader-follower technology has matured substantially over the years and is at a point where it can now be deployed, Frelk said. “The basic software … that has been demonstrated, in our opinion, doesn’t have a lot left to do before you begin to deploy it.”
However, there are still some challenges and room for improvement. These include the hardening of sensors and better integration between the vehicles and the onboard equipment, he said.
There are typically seven or eight vehicles in an autonomous convoy, Frelk said. They are all equipped with an autonomy kit and any of the vehicles can take over as the “leader” platform.
“There’s no requirement today that there will be a specific vehicle designated” as the lead platform, he noted.
Robotic Research is also working with the Army, the German Federal Ministry of Defence and Rheinmetall to support leader-follower technology with partner nations.
The U.S. Army wants “to expand this capability and make it interoperable with other vehicles … for convoy operations with allied forces,” he said.
While the Pentagon has shifted its focus from counterinsurgency operations to great power competition with adversaries Russia and China, Frelk said there is still a need for leader-follower technology.
“There is still going to be vulnerabilities to convoy operations and [a desire to] to reduce the number of deaths and improve … the functionality of moving things rapidly,” he said. “Leader-follower is going to be useful.”
Additionally, the autonomy packages that are being tested with the leader-follower program are not just relevant for convoy operations, Frelk said. The program has an impact on other vehicles including combat systems.
The same “autonomy kit that’s proved out on leader-follower is being deployed on other systems that are weaponized systems,” he said.
“Think of it as a springboard to combat vehicles and other vehicles being able to operate in GPS-denied environments autonomously.”
The basic software stack is portable and can be used with a variety of systems, but different platforms may require separate sensors, he noted.
For example, the autonomy needed for off-road operations will be different compared to on-road ops.
“It’s a tweaking of the system, not a whole new system,” he explained.
Besides working with the Army, Robotic Research also has contracts with other Defense Department components such as the Defense Logistics Agency, Frelk said. Last year, DLA awarded the company a contract to develop an unmanned autonomous guided vehicle to tow loaded carts inside and outside warehouses.
DLA has 20 storage sites and more than 570 warehouses, according to a Robotic Research press release. The development of the AGV could lead to follow-on contracts for as many as 100 vehicles.
The company is also working with the Defense Threat Reduction Agency on counter-weapons of mass destruction efforts, Frelk said.
Meanwhile, in late 2021 Robotic Research completed a $228 million Series A funding round to expand its commercial offerings. That will bear fruit for the military, Frelk said.
“The government gets to benefit from the number of miles that are being driven with similar autonomy capability and the lessons learned there,” he said.
Topics: Army News, Robotics and Autonomous Systems, Robotics
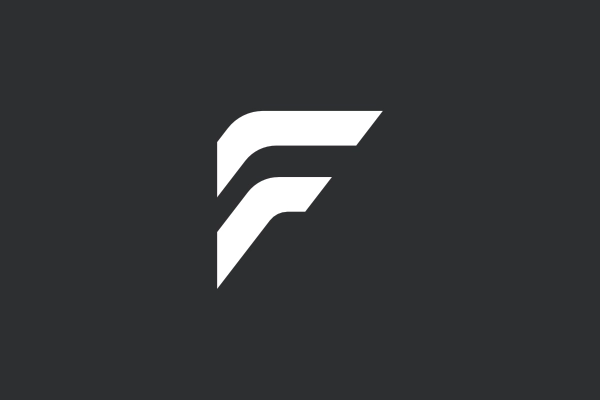
Softbank is pouring $228 million into a self-driving company targeting markets that much bigger opponents haven't touched
Robotic Research, cofounded in 2002 by CEO Alberto Lacaze and vice president Karl Murphy, is expanding its self-driving technology from military and defense uses into the needs of buses, trucks, and logistics through its commercial division, RR.AI. But Lacaze said what separates it from the other players tackling autonomous trucks for use on public roads is its focus on less regulated sectors. This includes off-road or dirt-road trucks, shuttles, and military and agricultural vehicles.
"There's a lot of applications you can deploy like that without having to fight regulators," Lacaze told Insider. "We are concentrating on those areas because they are the markets that are available right now."
SoftBank Vision Fund 2, Enlightenment Capital-led investment will enable the company’s commercial division, RR.AI, to scale and provide an end-to-end autonomy solution for transportation and logistics markets.
"Our plan is to out deploy most companies, at least in the verticals that we're working on," Lacaze added.
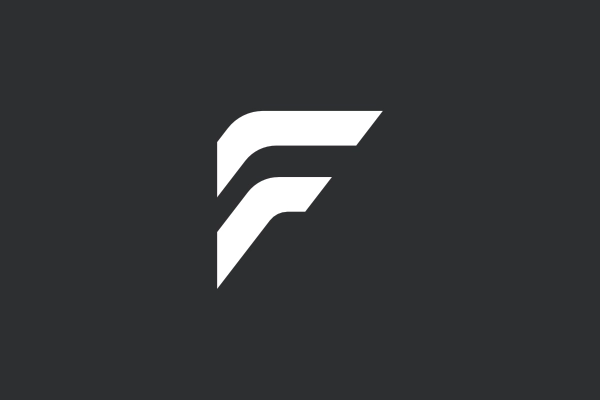
NFI and Robotic Research sign agreement to bring Automated Driving Systems to North American Transit Agencies
NFI and Robotic Research sign agreement to bring Automated Driving Systems to North American Transit Agencies
WINNIPEG, Manitoba, Aug. 12, 2021 (GLOBE NEWSWIRE) -- (TSX: NFI, OTC: NFYEF) NFI Group Inc. (“NFI” or the “Company”), a leading independent bus and coach manufacturer and a leader in mobility solutions, today announced an agreement with Robotic Research, LLC (“Robotic Research”) to increase the deployment of advanced driver-assistance systems (“ADAS”) in transit agency fleets across North America.
The agreement expands the partnership between New Flyer of America Inc. (“New Flyer”, an NFI subsidiary) and Robotic Research originally announced in 2019, and builds on the unveiling of North America’s first automated transit bus, the Xcelsior AV™, to pursue integration of Robotic Research’s AutoDrive® technology into new and existing public transit vehicles. The technology, which will incorporate Society of Automotive Engineers (“SAE”) Standard J3016 capabilities up to Level 4, will add ADAS features to help prevent pedestrian and cyclist collisions. Ultimately, automated vehicles (“AVs”) will contribute to improving road safety and lending the potential to shorten commute times, increase energy efficiency, and reduce congestion.
“For decades NFI has been a global leader in mass mobility, and we continue to lead the industry in the evolution and deployment of EV and AV technology,” said Paul Soubry, President and Chief Executive Officer, NFI. “Through our four pillar approach to mobility solutions – including buses and coaches, infrastructure, connected technology, and workforce development – we are enabling the new mobility era. Expanding our AV capabilities is a critical part of that vision and fits with our strategy to invest in high-growth areas.”
“Completing development of the first Xcelsior AV with Robotic Research demonstrates our continued leadership in innovation, and our commitment to developing and testing the best technology available,” said Chris Stoddart, President, North America Bus and Coach. “Our ADAS vision has always been to improve safety, efficiency, and accessibility through innovation, and, together with Robotic Research, we intend to expand AV capabilities across our full suite of public transit vehicles in North America.”
In addition to preventing collisions, Robotic Research’s AutoDrive® technology enables precision docking, enabling the bus to maneuver within inches of the level boarding platforms, increasing access for passengers with disabilities in accordance with Americans with Disabilities Act (“ADA”) rules. The technology can also enable “leader-follower” behavior, where multiple buses can be electronically linked together to help ease congestion at peak transit times.
“Our expanded partnership with NFI demonstrates a joint commitment to improving roadway safety by enabling technology to assist transit operators,” said Alberto Lacaze, President of Robotic Research. “The agreement will also help transit authorities save money by detecting and preventing accidents before they occur, which will address a major cost of insurance for transit agencies overall.”
The agreement marks NFI’s next stage of investment in ADAS technology, building on the completion of New Flyer’s Xcelsior AV™ unveiled in January 2021, New Flyer’s history-making pilot project with the Connecticut Department of Transportation (funded by the FTA's Integrated Mobility Innovation initiative), and New Flyer's launch of its Automated Technology Program first announced in May 2019.
Robotic Research is a U.S.-based, global leader in technology specializing in autonomy and platooning solutions for commercial and defense customers. Founded in 2002, the Company has been a trusted technology partner to the public and private sector for nearly twenty years, driven to make the way people move smarter, safer, and more efficient. For more information about Robotic Research, visit rr.ai.
NFI is a leader in zero-emission mobility, with electric vehicles operating or on order in more than 80 cities in five countries. Today, NFI supports growing North American cities with scalable, clean, and sustainable mobility solutions through a four-pillar approach that includes buses and coaches, technology, infrastructure, and workforce development. It also operates the Vehicle Innovation Center (“VIC”), the first and only innovation lab of its kind dedicated to advancing bus and coach technology and providing workforce development. Since opening late 2017, the VIC has hosted over 300 interactive events, welcoming 3,000 industry professionals for EV and infrastructure training. For more information, visit newflyer.com/VIC.
About NFI
Leveraging 450 years of combined experience, NFI is leading the electrification of mass mobility around the world. With zero-emission buses and coaches, infrastructure, and technology, NFI meets today’s urban demands for scalable smart mobility solutions. Together, NFI is enabling more livable cities through connected, clean, and sustainable transportation.
With 8,000 team members in nine countries, NFI is a leading global bus manufacturer of mass mobility solutions under the brands New Flyer® (heavy-duty transit buses), MCI® (motor coaches), Alexander Dennis Limited (single and double-deck buses), Plaxton (motor coaches), ARBOC® (low-floor cutaway and medium-duty buses), and NFI Parts™. NFI currently offers the widest range of sustainable drive systems available, including zero-emission electric (trolley, battery, and fuel cell), natural gas, electric hybrid, and clean diesel. In total, NFI supports its installed base of over 105,000 buses and coaches around the world. NFI common shares are traded on the Toronto Stock Exchange under the symbol NFI. News and information is available at www.nfigroup.com, www.newflyer.com, www.mcicoach.com, www.arbocsv.com, www.alexander-dennis.com, and www.nfi.parts.
Forward-Looking Statements
This press release may contain forward-looking statements which reflect the expectations of management regarding New Flyer’s and NFI’s strategic initiatives, plans, business prospects and opportunities, including the future existence and growth of a market for advanced driver-assistance systems (“ADAS”) in transit vehicles and the economic, efficiency, reduction in street congestion, safety and other benefits arising therefrom. The words “believes”, “views”, “anticipates”, “plans”, “expects”, “intends”, “projects”, “forecasts”, “estimates”, “guidance” and “targets”, “may”, “will”, and similar expressions, are intended to identify forward looking statements.
Although the forward-looking statements contained in this press release are based upon what management believes to be reasonable assumptions, investors cannot be assured that actual results will be consistent with these forward-looking statements, and the differences may be material. Actual results may differ materially from management expectations as projected in such forward-looking statements for a variety of reasons, including, market and general economic conditions and economic conditions of and funding availability for customers to purchase vehicles with ADAS; ADAS technology currently in existence has not yet been fully developed and tested for use in transit vehicle applications; ADAS vehicle regulations and standards have not yet been developed and implemented to permit fully autonomous transit vehicles to be operated in revenue service; there may not be sufficient customer demand for transit vehicles with ADAS, or at all, in order to commence or maintain the manufacture of such products; the expected economic, efficiency improvements, safety and other benefits described in this release for the communities, customers and passengers that operate and ride on transit vehicles with ADAS may not be as great as those anticipated or may not be realized at all; and the other risks and uncertainties discussed in the materials filed with the Canadian securities regulatory authorities and available on SEDAR at www.sedar.com. Due to the potential impact of these factors, NFI and New Flyer disclaim any intention or obligation to update or revise any forward-looking statements, whether as a result of new information, future events or otherwise, unless required by applicable law.
For media inquiries, please contact:
Lindy Norris
P: 320.406.3386
Lindy_Norris@newflyer.com
For investor inquiries, please contact:
Stephen King
P: 204.224.6382
Stephen.King@nfigroup.com
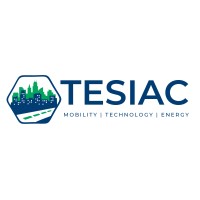
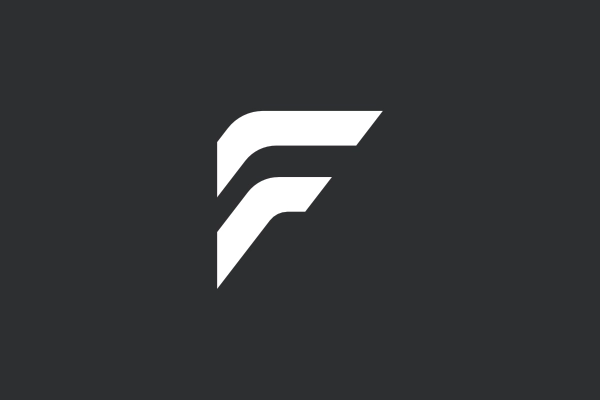
Robotic Research and TESIAC Announce Strategic Alliance to Revolutionize Urban Mobility
ROBOTIC RESEARCH AND TESIAC ANNOUNCE STRATEGIC ALLIANCE TO REVOLUTIONIZE URBAN MOBILITY
Relationship will advance future-proof, smart city, mobility options for public and private sectors
CLARKSBURG, Md.–(BUSINESS WIRE)–Robotic Research, a global leader in autonomous driving technology and solutions, announced today that it has formed a strategic relationship with Infrastructure-as-a-Service (IaaS) provider TESIAC to deliver advanced mobility options as part of a larger smart city offering to government and private industry customers.
“TESIAC’s ability to provide a comprehensive, continuously upgraded infrastructure solution that requires no initial capital outlay is a game-changer, not just for mobility, but for energy, operations, and management too,” said Eddie Mottern, Executive Vice President for Robotic Research. “We’re honored to form this strategic alliance and be TESIAC’s autonomy partner for this next-generation mobility offering.”
Robotic Research will be leveraging its extensive experience deploying autonomy solutions for the mass transit, trucking, first-last mile, and accessible transit markets, as well as its support of Programs of Record for the U.S. military, such as Expedient-Leader Follower. Thanks to its 19-year-long history working with the Department of Defense, Robotic Research has created one of the largest autonomous vehicle fleets in the world.
TESIAC will benefit from Robotic Research’s experience to execute on its mission of developing a solution set for smart city projects with mobility at its core. With the support of private capital investment from TESIAC’s capital partners, these projects will be developed with the client’s end goals in mind. Preparing for full autonomy is one of the critical elements of TESIAC’s technology continuum which, through private investment, provides customers with a peace of mind that solutions can be programmatically upgraded and will not become outdated or obsolete within the scope of a project.
“TESIAC focuses on scalable and integrated infrastructure to bring efficient and more effective practices to sustainable development,” said Karen Morgan, a Managing Partner at TESIAC; “And with its vast experience, Robotic Research will help TESIAC create an ‘innovation continuum’ to meet its’ clients objectives.”
TESIAC, Robotic Research, and Verizon are organizing partners of the Electric Mobility Symposium (EMS) to be held on June 24th, at Marine Corps Air Station Miramar, in San Diego. EMS brings together companies and technologies that make up this next-generation, smart city ecosystem, showing how 5G, autonomous mobility, electric vehicles, and microgrid technology unlock the clean, connected base of the future.
“It’s all about showing how these various technologies create an ecosystem that not only makes life better on a military base but can—and will—be replicated in the civilian world, with municipalities and private industry,” said Mottern.
About Robotic Research
Robotic Research is U.S.-based, global leader in localization, autonomy, and robotic technology transforming the way we move. Founded in 2002, the Company has been a trusted technology partner to the public and private sector for nearly twenty years. From people to platforms, at home or overseas, Robotic Research is driven to make the way you move smarter, safer, and more efficient.
To learn more about Robotic Research, visit www.rr.ai, and follow us on Twitter and LinkedIn.
About TESIAC
TESIAC is a Managed Services Platform that delivers Infrastructure-as-a-Service to public and private entities through flexible project management and innovative financial structures. TESIAC operates at the nexus of mobility, technology, energy, and capital markets. By doing so we enable integrated and interoperable systems to enhance overall efficiencies, increase operational performance, and create layers of sustainable value. TESIAC brings together an experienced interdisciplinary team and partners with new and advanced technologies. Our core principles are centered around smart city development with a focus on climate, social equity, and job creation.
To learn more about TESIAC visit www.tesiac.com.
Contacts
Robotic Research Contact
Taylor Smith
Press@rr.ai
TESIAC Contact
Emma Buls
emma.buls@tesiac.com
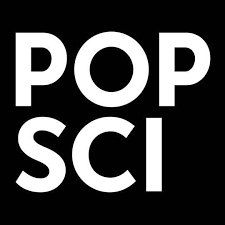
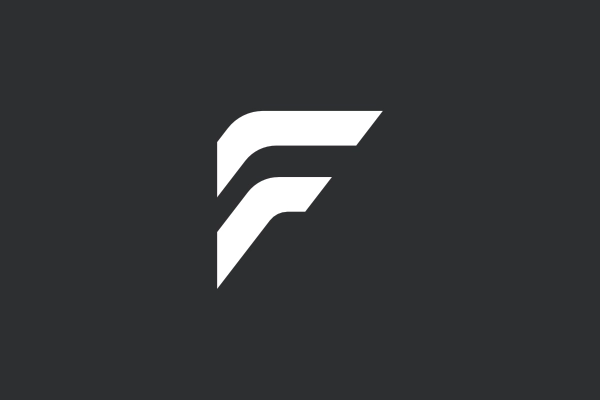
These multi-tasking machines can roll across the ground—or fly through the air Meet the Pegasus family of drones.
These multi-tasking machines can roll across the ground—or fly through the air
Meet the Pegasus family of drones.
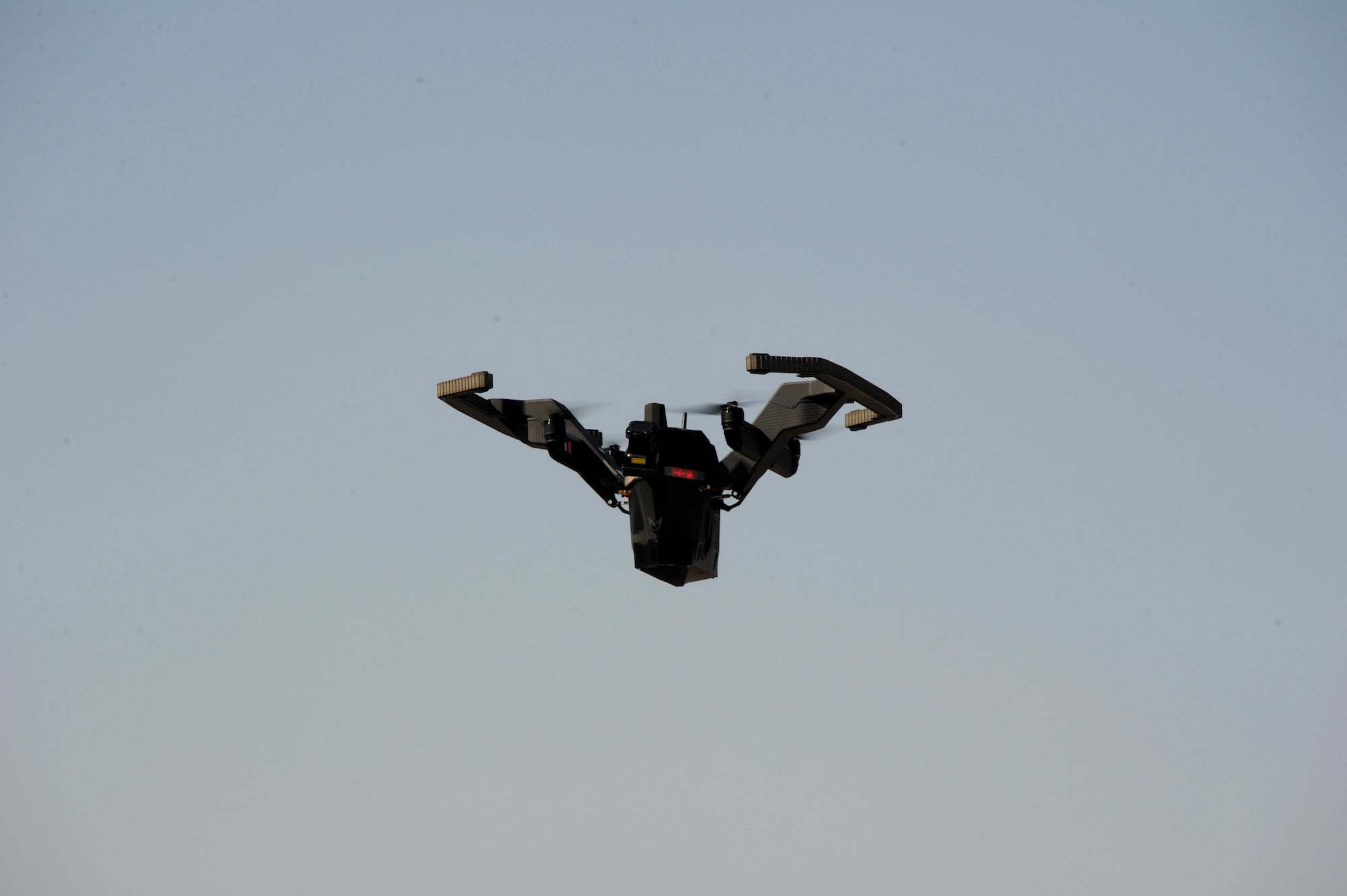
Behold the Pegasus! In September last year, the US Army tested the drone as part of Project Convergence, a big exercise exploring future machines of war. A photo reveals its matte-black form stark against the sky, a red light glowing in the middle of an obsidian fuselage.
“These vehicles fit a new category of robotic systems,” Alberto Lacaze, president of Pegasus-maker Robotic Research, said in a release from the Army about the event. “They aren’t quite ground vehicles, they’re not quite aerial vehicles—they’re somewhere in between.”
The Pegasus family of drones comes in three sizes, ranging from 4 to 38 pounds. The electric drones are all designed to fly between 20-30 minutes—or to drive for several hours on the ground. In the photo above, the tracks it can cruise on are lifted up like guardrails around its rotors.
Endurance in the sky and on the ground varies with battery size and airframe. The light Pegasus Mini is listed as having only 2 hours of drive time, whereas the larger Pegasus III can travel for up to 8 hours.
Building a multi-modal drone comes with certain design trade-offs. The weight of tracks on a quadcopter can limit endurance in flight, while accommodating rotors on a tracked vehicle means a more spread-out body than normally seen on military ground robots. What the combined design promises is the ability to get above, around, under, and through obstacles.
On tracks, a Pegasus could roll through a culvert and then, once on the other side, take flight, signaling if the passage is safe for humans to follow. When equipped with sensors, the drones can record and transmit video to human operators. If a Pegasus scouts an area and is successfully recovered (not always a guarantee in war), that information can be uploaded and used to generate a 3D map of what it recorded.
As billed, the drones can also operate in areas without GPS. That’s key because GPS can be actively denied by enemies using jammers (or disabling satellites, should a war escalate to the exchange of missiles in orbit), and it can also just be passively denied, by operating in terrain like mountains or caves that make it hard to receive signals.
In such situations, a robot that can scout and map terrain could prove especially valuable, as it restores an understanding of the area to a military accustomed to operating with GPS. Like many of the technologies tested in Project Convergence, the Pegasus family will likely undergo future testing and evaluation to see if the military will adopt it. What it does promise is a way to get both a ground and aerial scout into the same body. And one version is small enough to fit on a backpack.
Read more on Popsci.com.